Q&A
Q: How does ordering work for kits?
A: It is a multi-step process – here is how it works:
- First step is to request your free 30 minute online session to allow us to walk thru the designs and models to discuss what your goals are with the build. This is really cool.
- Add the selected boat kit deposit to your shopping cart. The payment process will ask you to acknowledge our Terms and Conditions prior to completion of your order. Once we receive confirmation of payment our internal process triggers fulfilment to get your kit ready. This also preserves your place in line for your kit. We are a FiFO company meaning first in, first out.
- Your order confirmation will also contain a link and login to the boat information page where you can find the study plans, drawings, and more information on your kit selection.
- The week prior to shipment we will reach out to complete the final payment payment required to release your order.
- As always, your deposit is fully refundable and tech support is always free.
Q: Why should I buy a Roosterfish Boat kit instead of retrofitting an older wooden boat?
A: You will spend far less time building our boat kit out than it takes to strip an older hull in preparation for retrofit. You will also likely find in the strip you have wood rot that must be replaced. The transom area is always suspect.
Q: It seems your boat kits are more expensive than others I have seen online. Why is this?
A: Our price itself does not tell the full story. Composites are inherently more expensive than plywood because they are man made from recycled and manufactured materials. The major benefit of this is they will not rot, mold, and are bug resistant – a huge bonus is they are also 30% lighter than plywood.
However, by using composites and precision machining techniques, our boat kits result in very strong assemblies and low build times. Since no fasteners are required as parts are tab glued together with 60,000 psi adhesives, the overall time to the water is greatly reduced. This methodology means expensive shop assembly time isn’t paid for as with dealer boats.
Q: How detailed are your build drawings?
A: Very detailed. As with our interlocking construction design, our drawings give the builder all the info they need.
Q: Since composites don’t have the density of wood, how do you fasten to it?
A: Composites require some additional support to attach items to it. Generally, holes are drilled and filled with epoxy where fasteners are then applied. When more rigidity or strength is required, fiberglass rod or backing plates may be glued into place and used to secure fasteners to. Our drawings will recommend such treatments where applicable.
Q: How does your after sales support work?
A: We offer 3 levels of support ranging from phone calls and emails to video conferences that walk our builders thru issues and questions. Other wood kit providers will sell plans or pre-cut plywood panels and a minimal set of drawings. As well as our engineering team support, you also have support from the engineering teams of our material suppliers to insure a quality build.
Q: I want something unique. Can this be done?
A: Sure, since we develop all of our own designs (not licensed from others) we can tailor a boat to the owners specifications. We will assist with the scope of work and create the necessary models and drawings required for manufacturing. Approval drawings are provided prior to the kit being ordered. A small fee is usually charged to cover some of the expenses of these changes.
Q: How much of your kits are recycled materials?
A: Great question! It varies but most designs have greater than half of its materials in recycled composite cores like PVC and PET. When laminated, they provide superior strength to weight ratios over other materials like wood. Don’t get us wrong, wood is very strong and makes great boats – it is also 30% heavier and is affected by rot and bugs if not properly sealed.
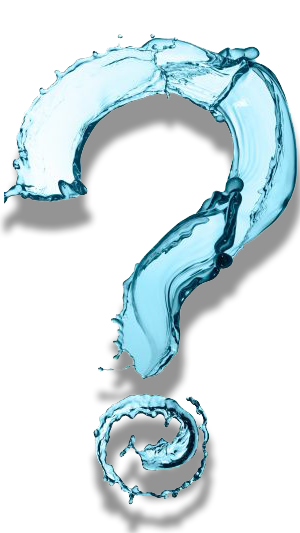